はじめに
電源回路設計においてパワーデバイスの熱設計は性能を左右する重要な要素です。
本記事では、電気系エンジニアが理解しやすいよう、熱回路モデルを活用した設計について解説します。具体的な数値計算と設計例を示し、すぐに活用できる実践的な内容を目指します。
熱設計の基礎
熱回路
電気回路と熱回路を対比させた表を示します。
この関係性が分かれば熱回路モデルは電気回路シミュレータで検証もできます。
電気回路 | 熱回路 |
電位 [V] | 温度 [℃] |
電位差 [V] | 温度差 [℃] |
電流 [A] | 熱流量 [W] |
抵抗 [Ω] | 熱抵抗 [℃/W] |
静電容量 [F] | 熱容量 [J/℃] |
熱回路モデル
熱回路モデルを考えるのにあたり以下のポイントをおさえましょう。
損失の発生源。電気回路的には電流源。
熱の流れに対する抵抗成分。パワーデバイスとヒートシンクなど異なる物体の接触面。
コンデンサで電気エネルギーを蓄えるように熱を蓄える要素。温度の過渡的な上昇時間に関わる。
具体的設計例(10kWコンバータ)
設計条件
- 非絶縁昇圧コンバータ
- 入力電圧 200V
- 出力電圧 800V
- スイッチング周波数 20kHz
- デバイス Infineon / IMZC120R012M2H
- 周囲温度 50℃
パワーデバイス特性
本記事では Infineon の IMZC120R012M2H を例に挙げます。
以下にデータシートから抜粋した主な特性を記載します。
メーカー | Infineon |
型式 | IMZC120R012M2H |
世代 | Cool SiC 第二世代 |
パッケージ | TO 247-4 |
耐圧 | 1200 V |
オン抵抗 \(R_{\text {ds(on)}}\) (25℃) | 12 mΩ |
オン抵抗 \(R_{\text {ds(on)}}\) (150℃) | 25 mΩ |
ターンON損失 \(E_{\text {on}}\) (175℃) | 789 μJ |
ターンOFF損失 \(E_{\text {off}}\) (175℃) | 362 μJ |
リカバリ損失 \(E_{\text {rr}}\) (175℃) | 770 μJ |
熱抵抗 (junction – case) \(R_{\text {th(j-c)}}\) | 0.24 K/W |
デバイス選定経緯(補足)
デバイス選定の経緯を補足しておきます。
耐圧ディレーティングは余裕をみて8割とすると、800V に昇圧するので 800V÷0.8=1000V が最低でも必要です。さらにスイッチングサージも加味して耐圧 1200V から選定しました。
Si MOSFET はせいぜい 750V 程度までのラインナップであり、オン抵抗が大きいため電流が大きい用途にはあまり向きません。その点は Si IGBT の方が優れますがスイッチング損失を少なくしたいと考え SiC MOSFET から選定することにしました。
具体的なデバイス選びとしては、世界的シェアの大きい Infineon から本記事執筆時で最新の第二世代 Cool SiC Gen2 から選びました。その中で耐圧 1200V で TO247 パッケージで最もオン抵抗が小さい 12mΩ を選びました。
以下に選定したパワーデバイスのホームページを掲載しておきます。
発熱量の計算
熱設計をするには熱源の把握が重要です。
損失計算の詳細はまた改めて別の記事にまとめたいと思いますので、ここでは簡易的な計算にしておき、熱設計の方を詳しく書いていきます。
回路電流
$$ 10 \mathrm{kW} \div 300 \mathrm{V} = 33.3 \mathrm{A} $$
導通損失
$$ P_{cond} = I^2 \times R_{ds(on)} = 33.3 ^2 \times 0.025 = 27.7 \mathrm{W} $$
合計スイッチング損失 [J]
$$ E_{sw} = E_{on} + E_{off} + E_{rr} = 789 + 362 + 770 = 1921 \mathrm{\mu J} $$
合計スイッチング損失 [W]
$$ P_{sw} = 1921 \mathrm{\mu J} \times 20 \mathrm{kHz} = 38.4 \mathrm{W} $$
合計損失
$$ P_{cond} + P_{sw} = 27.7 + 38.4 =66.1 \mathrm{W} $$
サーマルインターフェースマテリアル(TIM)
ヒートシンクなどの放熱器の表面には若干の歪みや微細な凹凸があります。
そのため発熱体のパワーデバイスにヒートシンクを直接取り付けると接触面の間に微細な隙間ができ、接触熱抵抗が高くなってしまい熱抵抗が大きくなってしまいます。
そこで、サーマルインターフェースマテリアル(Thermal Interface Materials:TIM)と呼ばれる熱伝導材料をパワーデバイス放熱面とヒートシンクの間に挟むことで、ヒートシンク表面の微細な隙間を埋めて接触熱抵抗を低減させます。
主にシート状のものは熱伝導シート、放熱シートとも呼ばれています。グリス状のものもあります。
ここでは TIM の熱抵抗は 0.1℃/W としておきます。
ヒートシンク
ヒートシンクはアルミ素材で自然空冷放熱とし、熱の対流に配慮して縦置き配置とします。ここではヒートシンクと空気間の熱抵抗を 0.5 ℃/W としておきます。この熱抵抗はどのような形状のヒートシンクをどのような向きで配置するかによって大きく左右します。
全体の熱抵抗
パワーデバイスのジャンクションからケース、TIM材、ヒートシンク、空気へと熱伝達する経路の熱抵抗を下表にまとめます。
ジャンクション・ケース間 | 0.24 ℃/W |
TIM材 | 0.1 ℃/W |
ヒートシンク・空気間 | 0.5 ℃/W |
熱等価回路
本検討の熱等価回路を以下に示します。
このように熱源を電流源、熱抵抗を抵抗器、周囲温度を電圧源で表します。
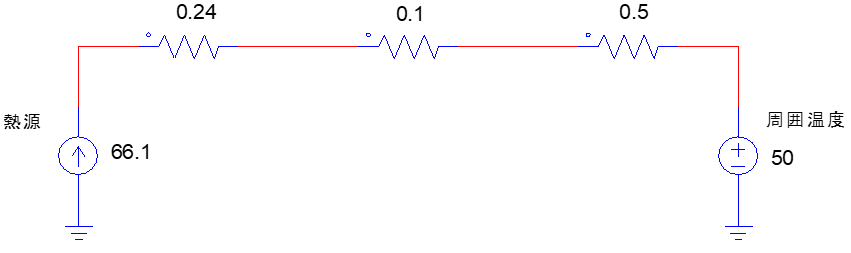
温度上昇計算
熱回路モデルを用いてパワーデバイスのジャンクション温度を計算します。
電流源からの電流が抵抗に流れることで電位差が生じるように、熱回路では熱抵抗の両端に温度差が生じるため、周囲温度に温度差を加えることでジャンクション温度を計算することができます。
全体の熱抵抗
$$ R_{th} = 0.24 + 0.1 + 0.5 = 0.84 \mathrm{ \mathrm{{}^\circ C} /W} $$
温度上昇
$$ \Delta T = P_{total} \times R_{th} = 66.1W \times 0.84 \mathrm{{}^\circ C} /W = 55.5 \mathrm{{}^\circ C} $$
ジャンクション温度
$$ T_{j} = T_{amb} + \Delta T = 50 \mathrm{{}^\circ C} + 55.5 \mathrm{{}^\circ C} = 105.5 \mathrm{\mathrm{{}^\circ C}} $$
以上より度がジャンクション温度は \(150 {}^\circ C \) を大幅に下回ることが確認できました。
まとめ
本記事では、10kWの昇圧コンバータを例に、熱回路モデルを活用したパワーデバイスの熱設計手法を解説しました。具体的な数値計算と設計例を通じて、すぐに実務で役立てられる内容を提供しました。設計時の参考にしていただければ幸いです。